Quick Overview – What’s Brewing at Steelbird?
- Steelbird is scaling up to manufacture over 60,000 helmets daily, all in-house.
- Plans are on to launch India’s first carbon fiber and fiberglass weaving facility for helmets.
- The brand is rolling out 15 new helmet models this year, with more coming every year.
- Targeting a massive jump in revenue: ₹1,300 crore by FY 2026-27.
Introduction: More Than Just Helmets, Steelbird Is Crafting a Movement
For most of us, a helmet is just a safety essential—but for Steelbird, it’s a passion project that’s evolving into a technological revolution. In an era where riders want style, substance, and smartness all in one gear, Steelbird is stepping up with a bold promise: helmets that protect and impress.
After 60 years in the industry, this isn’t just another growth story. It’s a redefining moment—where helmets are being seen not just as safety products, but as lifestyle essentials, blending innovation, fashion, and top-tier engineering.
Inside the Steelbird Ecosystem: Built In-House, Built for Safety
What makes Steelbird stand out isn’t just its scale—it’s the way everything is done under one roof.
No outsourcing. No compromise.
Every tiny part of the helmet—from shells, visors, EPS foam, and chinstraps to rivets, stickers, and bags—is crafted in-house. This ensures total control over quality, especially for a product meant to save lives.
“Even a tiny deviation can cost a life. That’s why we don’t outsource anything,” says Rajeev Kapur, Managing Director of Steelbird.
It’s this mindset that’s built trust with bikers in India and across 50+ countries where Steelbird exports.
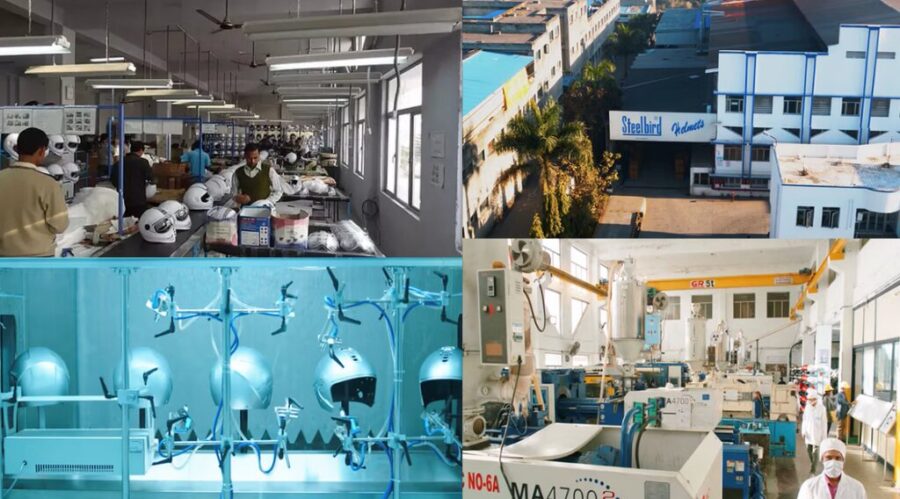
Growing Big, Thinking Bigger: Expansion in Motion
Steelbird recently completed a ₹54 crore expansion in FY24. And they’re already pumping in another ₹50 crore this year to further strengthen their machinery and plant capacity. The goal? To manufacture over 60,000 helmets daily. Yes, you heard that right!
Across its nine massive facilities—six in Baddi (Himachal Pradesh) and three in Noida (Uttar Pradesh)—the company now runs operations over a 1 million sq. ft. area.
And it’s not just about making more helmets—it’s about making them better and faster.
For instance:
- The EPS (impact-absorbing foam) plant currently produces 45,000 units a day.
- The decal plant prints 14,000 helmet stickers daily.
- Over ₹40 crore has already been spent on modernizing these operations.
The Carbon Fiber Revolution: Lighter, Stronger, Smarter Helmets
Steelbird isn’t stopping at plastic shells. It’s about to shake up the game with something India has never seen before—a dedicated carbon fiber helmet manufacturing unit, completely in-house.
Why does that matter?
Carbon fiber helmets are stronger, lighter, and offer far better impact resistance. Until now, most brands had to import these materials or get them made abroad. Steelbird is changing that.
They’re planning to weave their own carbon fiber and fiberglass, making it the first-ever in-house facility of its kind in India. This means:
- Full control over material quality
- The ability to create hybrid combinations and unique weave patterns
- Helmets that are not just light—but genuinely elite in strength and performance
What’s Coming: 15 New Helmets in One Year
Understanding today’s rider isn’t easy—they want safety like a soldier’s armor, the comfort of a cushioned cloud, tech that talks to their smartphone, and a design that turns heads at traffic lights. It’s not just about protection anymore—it’s about personality, performance, and presence on the road.
That’s why it plans to launch 15 new helmet models in FY25 alone.
Each helmet model takes anywhere between ₹1.5 crore to ₹10 crore in development costs and up to 2–3 years of R&D. That’s serious commitment.
From smart helmets with built-in tech to trend-forward designs that match a rider’s vibe, Steelbird is not just making helmets anymore—it’s creating experiences.
Quick Snapshot of Steelbird’s Big Picture
Metric/Plan | Details |
---|---|
Daily Helmet Production | 60,000+ units/day |
FY24 Capital Investment | ₹54 crore |
FY25 Capital Investment | ₹50 crore |
EPS Production | 45,000 units/day |
Decal Output | 14,000 decals/day |
FY24 Turnover | ₹787 crore |
FY25 Target | ₹1,000+ crore |
FY27 Goal | ₹1,300 crore |
Helmet Models Planned (FY25) | 15 new models |
Long-Term Launch Plan | 10 new models every year |
Key Innovation | India’s 1st in-house carbon fiber & fiberglass plant |
Conclusion: Steelbird’s Ride Has Only Just Begun
In a time when India is tightening helmet laws and riders are demanding more out of their gear, Steelbird is in the perfect gear—high, focused, and fearless.
This isn’t just about making more helmets—it’s about reshaping an industry. With its deep investment in technology, design, and in-house excellence, Steelbird is raising the bar for what helmets can be—smarter, stronger, and way cooler.
From roads in India to highways abroad, the Steelbird name is set to travel far—and fast. Because this isn’t just helmet production anymore. It’s a revolution on two wheels.